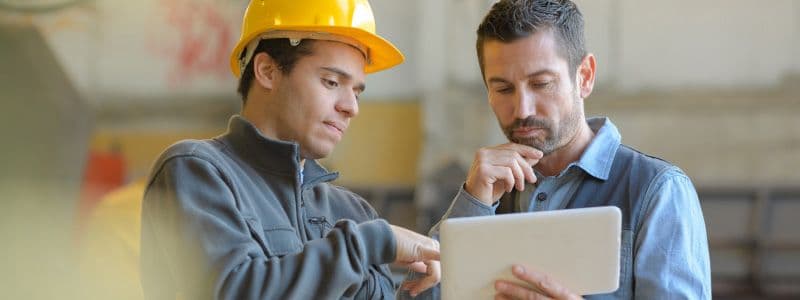
Truth, Transparency, and Trust
Keys to Successful Information SharingOne of the largest hidden costs in Facilities Management comes from external vendor costs -- specifically their labor and time. Specialized technicians for complex trades and projects may be brought in on an as-needed basis to support existing facilities teams. Their expert knowledge and specialization are useful for certain situations.
One of the main overlooked costs with external vendors is the time it takes for them to complete their work. A lot of these costs come from travel and waiting for information, including as-builts, equipment locations, correct filter sizes, or necessary tools. That downtime creates inefficiencies due to improper access.
ARC Facilities is helping to minimize these counterproductive trends by giving facilities teams control over their building information. With access to all their as-builts, mechanical drawings, and equipment locations from their devices, they can quickly and easily share data with external vendors. Visiting contractors are now able to arrive on-site prepared with the necessary building plans, equipment locations, and O&M documentation to amplify their operative productivity.
Facilities management thrives on collaboration, especially involving external specialists who address maintenance and repair tasks. The depth of their understanding of the facilities they work on can significantly impact the outcome of their efforts. Just as a compass is indispensable for navigation at sea, providing these specialists with detailed facility information upfront is essential for steering maintenance tasks toward success.
“Consider the actual scenarios where a lack of information leads to avoidable mishaps: a technician inadvertently strikes a water pipe while fixing a sewage line due to the absence of blueprints, or another spends hours searching for a water shut-off valve to change a simple fixture,” said Jonathan Fader, from National Facilities Direct who provides facility management services in all major industries.
“These incidents highlight the direct impact of information sharing on operational efficiency. Armed with detailed layouts, maintenance records, and asset information, external companies can swiftly identify and resolve issues, minimizing downtime and avoiding unnecessary revisits,” added Fader.
Safety and compliance are also key considerations connected with sharing information. In today's tightly regulated environment, ensuring that all maintenance and repair work adheres to safety standards and compliance regulations is paramount. Sharing detailed safety protocols and compliance requirements with external contractors upfront is crucial for mitigating risks and avoiding potential penalties.
Many facilities managers have expressed concerns about data security. Protecting sensitive facility information is as crucial as safeguarding a patient's medical records, necessitating secure channels for information exchange.
“Choosing the right external companies to share sensitive facility information with is critical,” said Fader. “This process is akin to selecting a crew for a nautical expedition; the wrong choice can lead to misdirection and increased risk, underscoring the importance of partnering with experienced and reputable service providers.”
Ensuring the transparent, concise, and accurate exchange of information is vital for aligning all parties, preventing costly misunderstandings and the need for rework. Sharing detailed information with external maintenance and repair companies emerges as a beacon, guiding us towards operational excellence.
This practice is not merely about preventing missteps but forging a partnership based on trust and transparency, where external companies become integral to the facility's ongoing success and resilience.
For ideas about sharing building plans with construction teams, check out our on demand webinar: 3 Ways To Tackle Your Project Closeout Challenges.