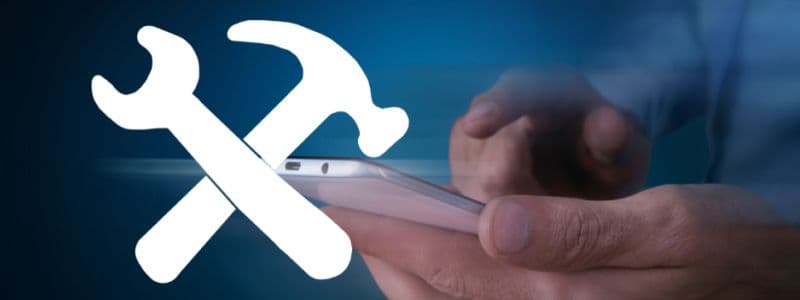
Maximizing Uptime:
The Power of Preventive Maintenance and Technology Integration in Facility ManagementPreventive maintenance refers to the systematic and scheduled maintenance activities performed on equipment, machinery, or facilities to prevent potential issues, breakdowns, or failures before they occur. The primary goal is to ensure that equipment remains in good working condition, minimizing the chances of unexpected breakdowns and its operational lifespan.
Key aspects include:
- Scheduled inspections: Conducting regular inspections to identify and address signs of wear, damage, or potential issues.
- Routine lubrication. Ensuring that moving parts are adequately lubricated to prevent friction-related wear and tear.
- Replacing worn parts. Timely replacement of components that are prone to wear such as belts, filters, or seals.
- Calibration and adjustment. Checking and adjusting settings to maintain optimal performance and accuracy.
- Cleaning and housekeeping. Removing dirt, debris, or other contaminants to prevent equipment malfunctions.
- Testing and Performance Monitoring. Conducting tests and monitoring performance indicators to identify deviations from normal operation.
Benefits of preventive maintenance include:
- Reduced downtime: Regular maintenance helps identify and address potential issues before they lead to equipment failure, minimizing downtime.
- Extended Equipment Lifespan. Proper maintenance contributes to the longevity of equipment, ensuring that it operates efficiently for a longer period.
- Improved Safety. Regular inspections and maintenance contribute to a safer working environment by addressing potential hazards and ensuring compliance with safety standards.
- Increased reliability. Regular maintenance enhances the reliability of equipment, reducing the likelihood of unexpected breakdowns.
- Optimal performance. Well-maintained equipment tends to perform at its best, providing consistent and reliable results.
The responsibility for preventive maintenance in facilities typically falls on the the facility or maintenance manager. This individual plays a crucial role in ensuring that all equipment, systems, and structures within a facility are well-maintained and operate optimally. Here are reasons why the responsibility is placed on them:
Expertise: Facility managers and maintenance personnel are trained and experienced in understanding the intricacies of various systems and equipment within a facility. They possess the necessary technical knowledge to perform maintenance tasks effectively.
Coordination: Facility managers are responsible for coordinating and scheduling maintenance activities. They ensure that preventive maintenance tasks are carried out systematically, minimizing disruption to normal operations.
Resource Allocation: Facility managers oversee allocating resources, including personnel, time, and materials for maintenance activities. They need to prioritize preventive maintenance tasks based on the equipment and systems.
Budgeting: Facility managers are often involved in budget planning. They allocate funds for preventive maintenance activities, ensuring that there are adequate resources to address routine maintenance needs and reduce the risk of unexpected breakdowns.
Compliance and regulations: FMs are responsible for ensuring that the facility complies with safety and environmental regulations.
Asset management: Facility managers manage the overall asset management strategy. They need to assess the condition of assets, plan for replacements or upgrades, and implement preventive measures to extend the lifespan of critical equipment.
Risk management: Preventive maintenance is a key component of risk management. Facility managers identify potential risk associated with equipment failure and take proactive steps to mitigate these risks through scheduled maintenance.
Communication: Facility managers often act as a liaison between different departments within an organization. They communicate with operations teams to understand equipment usage patterns and collaborate with maintenance teams to ensure that preventive maintenance aligns with operational needs.
Preventive maintenance is a multi-faceted task that requires technical expertise, coordination, resource management, and compliance adherence. Facility managers are well-positioned to take on this responsibility as part of their broader role in overseeing the safe functioning of a facility.
There are various tools and technologies available to facilitate the effective planning and execution of these activities. These tools help streamline processes, improve efficiency, and enhance the overall maintenance strategy.
Facilities teams involved in preventative maintenance often rely on various technologies to enhance their efficiency and effectiveness, including:
Mobile Applications for Field Technicians: Mobile apps provide field technicians with on-the-go access to relevant information and documentation. Technicians can use these apps to receive real-time updates on maintenance tasks, access equipment manuals and report issues directly from the field. Mobile applications enhance communication, streamline workflows, and improve the overall responsiveness of facilities teams.
Internet of Things (IoT) Sensors and Devices: Sensors can be installed on equipment and assets to monitor their performance in real-time. These sensors collect data on factors such as temperature, vibration, and energy consumption. By analyzing this data, facilities teams can detect potential issues before they lead to equipment failure. IoT devices contribute to predictive maintenance strategies, allowing teams to intervene early and avoid costly repairs.
Computerized Maintenance Management System CMMS. A CMMS is a software solution that helps facilities teams organize, schedule, and track maintenance activities from desktop computers.
Mobile applications and CMMS can work seamlessly to enhance facility maintenance processes. Here’s how they can complement each other:
Real-Time Access to Information: Mobile applications provide field technicians with CMMS data while on-site. Technicians can view preventive maintenance schedules, work orders, equipment history, and any relevant documentation right from their mobile devices. This real-time access ensures that technicians have the most up-to-date information to perform maintenance tasks effectively.
Barcode/QR Code Scanning. Mobile apps equipped with barcode or QR code scanning capabilities can simplify the identification of equipment and assets. Technicians can use their mobile devices to scan equipment codes, instantly accessing maintenance histories and manuals. This accelerates the maintenance process and improves accuracy in data retrieval.
Documentation and Photo Capture: Mobile applications enable technicians to capture photos, record videos and observations, and update documentation directly from the field. Visual documentation is valuable for troubleshooting and analysis.
Offline Capabilities: In facilities where internet connectivity may be intermittent, mobile apps with offline capabilities allow technicians to continue working and recording data even without a network connection.
These technologies collectively empower facilities teams to move from a reactive maintenance approach to a proactive one, reducing downtime, minimizing equipment failures, and optimizing the overall performance of the facilities they manage.