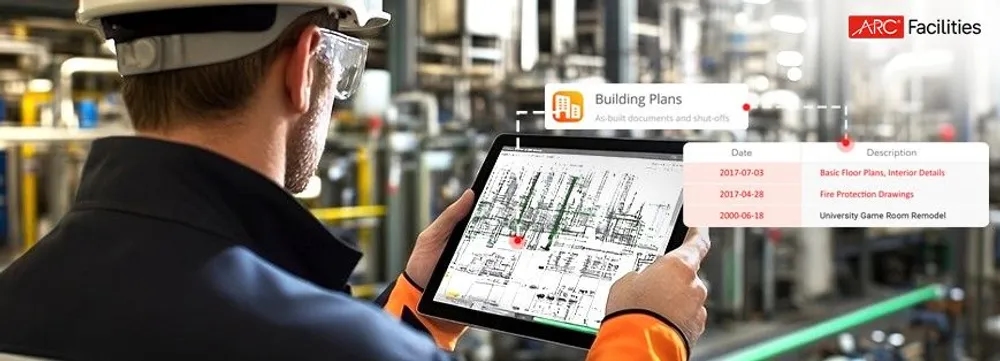
Data-Driven Facility Management
Why Facility Data is EssentialIn the field of facility management and building maintenance, informed decision-making can have a big impact on cost reduction, mitigating emergencies, and extending asset lifespan.
Budget constraints and limited resources often make decision-making challenging in facility management. However, by leveraging data-driven insights, facility managers can prioritize essential tasks, optimize resource use, and ultimately achieve the best possible outcomes. Access to real-time data on asset performance, maintenance needs, and resource allocation empowers businesses to make informed choices that balance operational efficiency with budgetary limits. This approach not only addresses immediate facility needs but also fosters long-term cost savings and operational resilience.
Dive into this blog to gain a deeper understanding of why data-driven facility management is becoming necessary in the world of facility operations and maintenance.
Optimizing Facility Operations: The Role of Data-Driven Facility Management Systems
Data-driven facility management is transforming how enterprises manage and control their physical assets, spaces, and infrastructure. By leveraging data analytics, facility management systems offer advanced tools for planning, tracking, and optimizing various aspects of facility operations. These systems use critical building data to streamline processes such as equipment tracking, asset management, maintenance scheduling, work order management, vendor coordination, and resource allocation. In industries like commercial real estate, healthcare, education, manufacturing, and government, data-driven facility management ensures more efficient operations, helping organizations make informed decisions and improve overall performance.
Studies show that predictive maintenance based on data insights can reduce downtime and costs in sectors like healthcare and manufacturing (Occupational Health & Safety). Real-time monitoring of safety conditions has led to safer environments and better compliance, especially in government facilities (American Society of Safety Professionals). By analyzing usage and vendor performance data, facilities can allocate resources more effectively, improving efficiency in industries such as commercial real estate and education (Gartner Research).
Importance of Data-Driven Facility Management
1. Enhanced Decision-Making
Accurate and comprehensive facility data provides managers with the insights needed to make informed decisions. Access to historical building data, current maintenance schedules, building maps, compliance documents, and emergency plans enables facility managers to identify trends and anticipate future needs.
For instance, with access to historical building data, facility managers can analyze past maintenance patterns to prevent recurring issues. By reviewing current maintenance schedules, they can allocate resources more efficiently to avoid service interruptions. Detailed building maps and compliance documents help ensure safety by enabling quick identification of emergency exits and shutoff locations. Meanwhile, up-to-date emergency plans allow facility managers to prepare effectively for emergencies, reducing response times and minimizing potential risks.
2. Improved Operational Efficiency
Facility management software relies on real-time data to streamline operations. By leveraging data on asset performance and maintenance history, organizations can optimize resource allocation, reduce downtime, and ensure timely maintenance, ultimately enhancing overall efficiency.
3. Strategic Planning
Data-driven insights are crucial for effective long-term facility planning. By analyzing historical data, facility managers can predict future needs, such as occupancy changes or maintenance demands, and proactively plan expansions or renovations. This data also enables precise budget allocation by highlighting high-cost areas and prioritizing investments that improve efficiency, reduce downtime, and extend asset lifespans. For example, Informatics INT reports that predictive maintenance and historical data use can cut maintenance costs by 25-30%, underscoring how data aids strategic decisions in facility management.
4. Compliance and Risk Management
Effective facility management software offers centralized record-keeping, automated reminders, and regulatory updates, augmenting compliance management. Additionally, it facilitates preventive maintenance and makes emergency response swifter, safeguarding both the organization and its occupants.
5. Preventive Maintenance and Cost Savings
Implementing preventive maintenance for assets can significantly reduce costs by addressing issues before they become costly repairs. It enables facility managers to understand when to conduct routine inspections, recondition, and replace parts of facilities and equipment, ensuring optimal performance and extended lifespan.
6. Asset Lifecycle Management
Facility data helps track the entire lifecycle of assets, from procurement to disposal. Managers can access equipment data, understand their condition, schedule timely repairs or replacements, and extend asset life, ultimately reducing capital expenditures.
7. Enhanced Collaboration Through Centralized Information
By housing all critical building documents in one easily accessible platform, teams can collaborate more effectively, reducing miscommunication and ensuring everyone has access to the latest updates.
8. Emergency Preparedness
Having immediate access to critical facility data, such as shut-off points, emergency equipment, and evacuation plans, enables facility managers to act fast during emergencies. This quick access helps control leaks, locate potential hazards, and prevent minor issues from escalating into major incidents, ultimately minimizing potential damage and ensuring safety.
9. Maintenance Predictability
In predictive maintenance, data analytics plays a critical role in avoiding unexpected breakdowns. Studies show that predictive maintenance, when effectively implemented, can prevent a significant number of such breakdowns. According to reports, predictive maintenance strategies can help manufacturing plants reduce downtime by as much as 20-25% and increase equipment uptime by up to 15%.
Moreover, maintenance managers are finding that having access to predictive analytics enables them to address potential failures before they happen, resulting in smoother operations and improved productivity.
10. Boosting Productivity with Smart Technology
Empower teams with mobile access to as-built plans, O&M documentation, and emergency data. By eliminating the need to search through physical records, teams can focus on completing more work orders and enhancing overall productivity.
The high-rise buildings and complicated workspaces have increased the pressure faced by facility managers. Managing utilities, scheduling repairs, handling vendor relationships, and ensuring workplace safety are demanding tasks that are difficult to manage manually. However, handling all these duties manually is nearly impossible.
This is where data-driven facility management systems play a crucial role. By leveraging real-time facility data, these systems empower organizations to make informed decisions, optimize operations, and enhance safety and cost-effectiveness. From predictive maintenance to emergency response, data-driven insights offer facility managers a competitive edge in managing and maintaining their facilities more efficiently. As technology advances, the integration of data analytics into facility management continues to streamline processes, optimize resource allocation, and future-proof operations for sustained success.
Take control of your facility management with ARC Facilities' smart building app. Instantly access critical building data from anywhere, optimize asset maintenance, monitor equipment, and reduce costs effortlessly. Request a demo today and discover how ARC Facilities can help you stay ahead, improve operational efficiency, and mitigate risks across industries.